23 марта 2018 г.
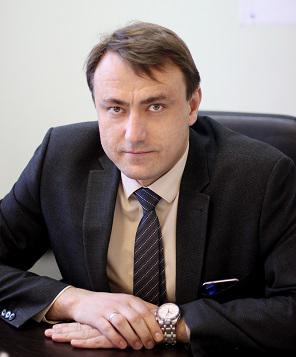
23.03.2018
Вице-президент РЭП Холдинга по оптимизации и развитию производства Алексей Горин
Самая высокая доля импорта приходится на станко- и машиностроение, и, в частности, на энергетическое машиностроение. В соответствии с принятыми правительством РФ планами, к 2020 году импортозависимость должна быть сокращена с 88 % до 40 %, в том числе через локализацию.
На повестке дня – модернизация отечественной экономики, направленная на развитие и повышение конкурентоспособности производства через политику импортозамещения и локализации. Сегодня российские компании, занимающиеся производством оборудования, не только создают новые технологии и продукцию, но и новые механизмы управления.
Одна из них - РЭП Холдинг, который воплощает свои планы по локализации производства газотурбинной установки MS5002E, входящей в состав газоперекачивающего агрегата нового поколения «Ладога-32». В рамках реализации этой программы 2017 год стал знаковым: специалисты компании освоили производство наиболее технологичных и наукоемких узлов и деталей турбины. Об особенностях проекта, его значении для компании и для отрасли в целом и о дальнейших шагах в этом направлении рассказывает вице-президент РЭП Холдинга по оптимизации и развитию производства Алексей Горин.
Алексей Александрович, расскажите, какая работа уже проведена холдингом в рамках локализации ранее, в предыдущие годы?
К 2014 году у нас практически полностью были завершены три из четырех этапов локализации. Первым шагом стало освоение агрегатирования газотурбинной установки (ГТУ) и рамы вспомогательных устройств (РВУ), всей электрической и трубной обвязки, далее освоен выпуск корпусных элементов, начиная с литья и заканчивая финишной механической обработкой, освоено изготовление дисков ротора турбокомпрессора с окончательной сборкой и балансировкой на модернизированном балансировочном оборудовании. На сварочных площадках освоено изготовление сварных конструкций, таких как РВУ ГТУ, входного патрубка, полностью освоено изготовление кожуха шумоизоляции с пакетированием. Для заводских испытаний ГТУ MS5002E на Невском заводе построен уникальный испытательный стенд.
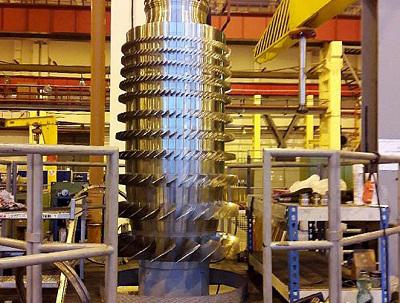
Таким образом, мы достигли предельного уровня локализации, определенного лицензионным соглашением на тот период времени: неосвоенными остались только компоненты горячей части турбины и проточной части компрессора.
Более глубокая локализация производства стала возможной благодаря достигнутым договоренностям с компанией GE о передаче полного комплекта документации, включая горячую часть турбины. Соответствующее соглашение с GE Oil & Gas было подписано в конце 2014 года – это ознаменовало начало четвертого, завершающего этапа локализации. Важно отметить – получение полного комплекта технической документации, включая горячую часть на индустриальную газовую турбину, это беспрецедентная сделка, которая дала нам возможность предложить рынку конкурентоспособный продукт без иностранного участия.
Каковы были предпосылки активизации программы локализации производства?
Принципиально два фактора подтолкнули нас к ускорению темпов локализации. Первый - это существенный рост курса иностранных валют, что привело к удорожанию компонентов, закупаемых за рубежом. Второй фактор – возрастающие риски, касающиеся бесперебойных поставок от европейских поставщиков. В совокупности эти факторы сделали задачу развития собственного производства и расширения пула российских и азиатских партнеров не просто главной целью, но и задачей, которая должна быть реализована в кратчайшие сроки.
При этом хочу подчеркнуть, что мы не ставим перед собой задачу 100% локализации в собственном производстве. Нам важно обеспечить надежность и предсказуемость работы наших агрегатов на жизненном цикле для заказчиков, а способы достижения данной цели могут быть различными.
Какие именно компоненты планировалось локализовать в 2017 году?
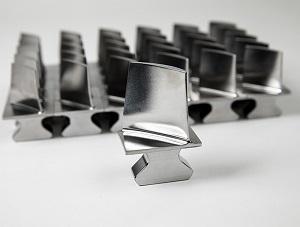
Совет директоров АО «РЭП Холдинг» поставил задачу за год освоить производство и изготовить опытные образцы ротора осевого компрессора и турбины высокого давления, полный комплект компрессорных ( на фото слева) и турбинных лопаток, элементы камеры сгорания, включая торцевую крышку с топливными форсунками, комплект подшипников ГТУ, систему автоматического управления (САУ). Причем в части САУ ГТУ стояла задача изготовить ее с использованием исключительно российской компонентной базы. Что касается турбинных лопаток, то в настоящее время мы осуществляем механическую обработку и нанесение износостойких и термобарьерных покрытий на базе отливки, полученной от иностранного производителя. Возможность и целесообразность организации литья лопаток нами изучается совместно с коллегами из ПАО «Газпром», Минпромторга и Минэнерго РФ.
Как удалось завершить проект в сжатые сроки? Каковы сложности, связанные с его реализацией?
Есть ряд специализированных технологий и производств, например – нанесение покрытий, глубинное шлифование, перфорация охлаждающих отверстий, которыми Невский завод (промышленная площадка РЭП Холдинга) в настоящее время не располагает. Поэтому проект реализовывался в тесной кооперации с отечественными предприятиями. Это стало возможным благодаря созданию на территории России уникальных новых производств.
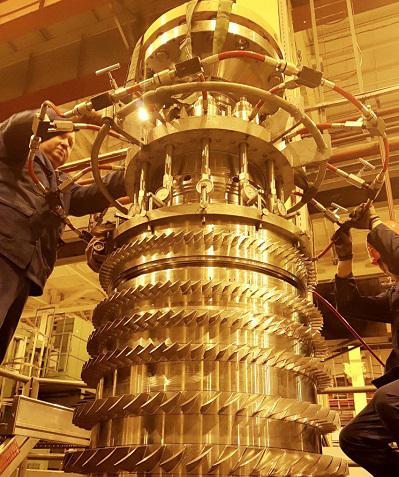
В целом для выполнения проекта было привлечено более 20 соисполнителей – отечественных промышленных компаний. Хотел бы отметить ООО «Пумори-Энергия», выполнившее работы по механической обработке лопаток компрессора, АО «РОТЕК», с которым мы сотрудничали в области нанесения износостойких и термобарьерных покрытий. ОАО «Уралтурбо» хорошо себя зарекомендовало в мехобработке направляющих лопаток турбины, «ПТК Электросталь» осуществляло механическую обработку рабочих лопаток турбины.
Для изготовления наиболее сложного узла камеры сгорания – торцевой крышки с топливными форсунками было задействовано АО «КМПО». Вся механическая обработка основных элементов топливных форсунок была сделана силами Невского завода, а «КМПО» осуществляет финишную сборку с применением электронно-лучевой сварки и вакуумной пайки.
Что касается ротора осевого компрессора, то можно сказать, что он изготовлен с наибольшей степенью локализации, то есть «от руды»: «ОМЗ–Спецсталь» специально для нас и в кратчайшие сроки освоило литье и ковку дисков ротора из иностранной марки материала, а механическая обработка лопаток и дисков, включая финишную сборку и балансировку, была выполнена на Невском заводе.
Как осуществлялся контроль качества и испытания локализованных компонентов?
Требования к контролю качества, а также сертификации и организации производства компонентов на новых мощностях подробно описаны в технической документации лицензиара. Например, для ответственных деталей, таких как лопатки турбины, предусмотрены процедуры аттестации первого образца (FPQ), в ходе которых произведенные образцы проходят не только все необходимые неразрушающие тесты (например, рентген, ЛЮМ контроль, КИМ), но и разрушающие – детали режут на образцы для микрографического исследования, испытаний на разрыв и т.д. И только после получения требуемых результатов по геометрии и наличию допустимого уровня дефектов, возникающих при литье и мехобработке, можно приступить к изготовлению пилотной партии (PLQ) – что подразумевает более глубокий контроль неразрушающими методами для 100% объема заготовок. По результатам контроля компонентов FPQ и PLQ принимается решение о возможности производства компонентов или необходимости доработки технического процесса. По сути РЭП Холдингу пришлось выполнять данные процедуры для всех компонентов, так как они производились впервые.
Требования к методикам и стандартам применяемого контроля также очень высоки и опираются на иностранные стандарты. Магнитно-люминесцентный контроль, проникающий люминесцентный контроль, микрографические исследования, жесткие допуски на чертежах, предполагающие сплошной контроль геометрии на специализированных установках КИМ, – все это было определённым вызовом для служб лаборатории Невского завода и отдела технического контроля, также как и для соответствующих служб наших подрядчиков. Нужно отметить, что, несмотря на жесткие и «непривычные» требования иностранных стандартов, наши специалисты справились и выполнили все поставленные перед ними задачи.
С целью максимального снижения технических рисков мы приняли решение расширить стандартные требования GE, предъявляемые к первым образцам, и определили дополнительный комплекс испытаний с привлечением специалистов и испытательной базы одного из ведущих российских институтов энергетического машиностроения «НПО ЦКТИ».
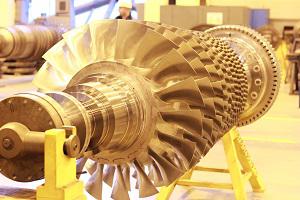
Проведенные испытания компрессорных лопаток на длительную прочность (HCF-тест) подтвердили качество материала и процессов обработки. Помимо этого в ЦКТИ были проведены натурные комплексные динамические испытания опорного подшипника с полуторакратной нагрузкой на всех необходимых режимах, в которых ему предстоит работать.
Для сертификации РЭП Холдинга, как производителя комплекта подшипников ГТУ, для лицензионного рынка была разработана целая программа квалификации, в которую входит не только динамический тест, но и проверка дизайна конструкции и материалов при проектировании, а также контроль процессов производства, таких как нанесение баббита на сегменты подшипников, который производится во Флоренции непосредственно специалистами GE Oil & Gas с привлечением иностранных лабораторий. Для справки, иностранные производители ГТУ часто не производят подшипники, а заказывают их в сторонних организациях. В отечественной же школе другой подход, и РЭП Холдинг останется верен ему – это один из компонентов независимости от сторонней, в нашем случае американской, компании.
Что касается разработанной нами системы автоматического управления, испытания ГТУ под ее управлением были проведены на испытательном стенде Невского завода. После чего было принято решение об установке данной системы на одном из газоперекачивающих агрегатов производства РЭП Холдинга в составе КС «Малоперанская» на магистральном газопроводе «Бованенково-Ухта» в режиме опытно-промышленной эксплуатации – система работает уже с декабря прошлого года.
Относительно локализованного ротора и других элементов турбины в начале прошлого года ПАО «Газпром» предоставил возможность проведения длинноцикловых натурных испытаний локализованных узлов на ГПА производства РЭП Холдинга на одной из действующей станции магистрального газопровода «Ямбург Тула 1» - КС «Вавожская».
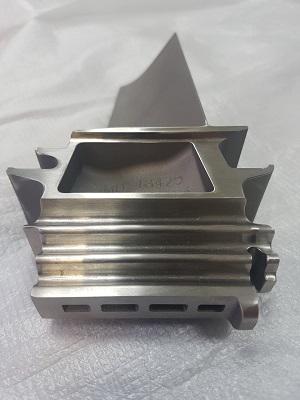
Монтаж локализованных узлов и деталей синхронизирован с программой технического обслуживания и ремонта ПАО «Газпром» – текущая наработка ГТУ составляет 24 000 ЭЧН и по состоянию на текущий момент
агрегат уже выведен на регламентное обслуживание. В срок до 1 апреля должны быть завершены все работы по техническому обслуживанию и монтажу локализованных узлов.
Расскажите об особенностях данного этапа локализации. В чем его уникальность?
Проект не имеет аналогов по своей сути, поскольку в нашей стране до сих пор не было опыта локализации горячей части индустриальных газовых турбин. Он интересен и тем, что в нем, как я уже упоминал, объединились усилия большого количества российских компаний, привлеченных в качестве соисполнителей.
Наша особая гордость - это комплект подшипников ГТУ, которые мы самостоятельно разработали и изготовили с применением российских марок материалов, что позволило отказаться от аналогичной продукции иностранного производителя. И это уже не просто локализация, это свой отечественный продукт. Шкаф системы автоматического управления ГТУ полностью спроектирован нашими инженерами на российской компонентой базе на основании оригинальных алгоритмов управления газовой турбиной.
Каковы дальнейшие планы холдинга в направлении локализации производства?
Самая главная задача локализации для нас – это сертификация российских поставщиков на высокоточное литье турбинных лопаток. Сложность заключается в необходимости строгого соответствия нормам лицензионного соглашения, а значит освоение иностранных жаропрочных марок материалов на никелевой и кобальтовой основе, и такого опыта в России практически нет. На текущий момент мы уже выбрали подрядчика, который будет заниматься освоением литья рабочих и направляющих лопаток ТНД. Поставка сертификационного комплекта запланирована на 1 полугодие 2019 года. В ближайшее время планируем окончательно определиться с выбором подрядчиков по литью лопаток турбины высокого давления (на фото слева).
На ближайший год мы ставим задачу полностью завершить локализацию камеры сгорания – нам осталось освоить изготовление жаровой трубы и переходной секции, дисков турбин высокого и низкого давления, а также завершить локализацию систем управления вспомогательным оборудованием: САУ топливного клапана, системы вибрации и системы контроля пульсации.
И, конечно же, отдельным направлением является проработка организации участка восстановительного ремонта компонентов горячего тракта.
Каково значение локализации компонентов турбины MS 5002E в рамках общей стратегии холдинга?
Локализация производства решает две очень важные задачи. Во-первых, это позволит снизить себестоимость изготовления и сервисного обслуживания ГТУ, а во-вторых работа по локализации развивает наш инженерный потенциал – формируется кадровое ядро конструкторов и технологов в области газотурбинного оборудования, не уступающих по уровню квалификации нашим иностранным партнерам.
Важно, что наши конструкторы и технологи, участвуя в процессах локализации, перенимают передовой опыт лицензиаров, повышают квалификацию и знания в области проектирования газовых турбин, которые в свою очередь будут востребованы в дальнейших проектах. В числе стратегических задач РЭП Холдинга - разработка собственной газотурбинной установки в сегменте 30-70 МВт.
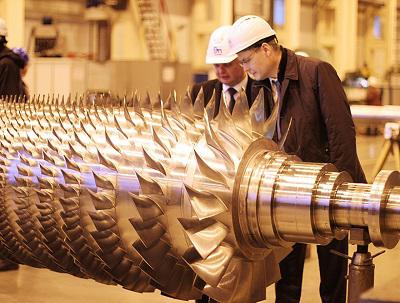
Индустриальные газовые турбины такого диапазона мощности в России еще не производят, и мы планируем занять эту нишу. Они могут быть востребованы и на объектах газотранспортной системы, и на объектах сжижения природного газа, и в энергетике, и в других областях, где необходимо надежное, эффективное и ресурсосберегающее оборудование.
Беседовала Ирина Королева
Перепечатка материала возможна при условии активной ссылки на EnergyLand.info